치수 공차란 무엇이며 공차 관리란 또 무엇을 의미하는 것일까요? 정밀한 혹은 정밀함을 요하는 기계 가공품을 다루는 설계과정 중에 공차는 항시 고려해야 하는 설계 주요 사항 중 하나입니다. 이제 막 설계를 시작한 신입 설계자에게 있어서 공차 관리란 용어 자체고 필요 이유에 대한 의문점을 가질 수 있습니다. 왜 공차를 관리해야 하는지를 이해하고 접목한다면 오류를 줄이고 보다 향상된 부품 설계가 가능해집니다. 이러한 본문 내용에 앞서 관련 용어에 대한 의미를 살펴볼 필요가 있습니다.
용어 정리
(1) 치수(Dimension)란 : 공간상에서 크기를 나타내는 수치를 말하며 길이 높이를 총칭하는 단어입니다. 도면상에 직접적으로 표기되는 수치를 말합니다.
(2) 공차(Tolerance)란 : 허용하는 오차 범위를 말합니다. 아래 그림의 정사각형과 원에 형상의 치수가 표기되어 있으며 이해를 돕기 위한 임의의 허용 공차가 기재되어 있습니다. 그림 상에서 공차를 통해서 확인할 수 있는 몇 가지 사실이 있습니다. (단위는 mm 적용)
- 정사각형의 가로 방향 정 치수는 400mm 입니다. 허용 공차가 최대 0.03mm, 최소 -0.05이므로 가공 후 허용할 수 있는 가로 방향의 치수는 최대 400.003mm (400+0.03) 이며 최소는 399.95mm (400-0.05) 입니다.
- 정사각형의 세로 방향 허용 치수는 최대 400.001mm (400+0.01) 최소399.99mm (400-0.01) 입니다.
- 원형 형상의 치수에 끼워맞춤 공차가 적용되어 있으며 느슨한 맞춤을 적용하여 e7을 적용하였습니다. (끼워맞춤 공차에 대해서는 차후에 포스팅 예정)

위의 두가지 용어정의를 바탕으로 치수 공차가 가지고 있는 의미를 풀어서 해석하면 다음과 같이 기술할 수 있습니다.
치수 공차란 가공을 통해 얻어진 가공 결과물의 수치상에 허용 오차범위를 말합니다. 가공 수치상에 허용 오차가 발생하는 이유는 무엇일까요? 설계의 결과물인 도면상의 정치수를 형상에 기재하더라도 소재를 가공하는 과정 즉 실물 가공 시에는 가공 오차가 발생하게 됩니다. 소재에 따라서 가공 방법에 따라 혹은 주물인지 판금물인지, 레이저 가공인지 여러가지 요인에 따라서도 공차 범위는 들쭉날쭉 하게 됩니다. 아무리 정밀하게 가공한다 하더라도 1/100, 1/1000 단위로 치수는 오차가 발생하게 됩니다. 도면상에 표기된 치수는 가장 이상적인 치수이지만 실제 결과물 자체는 완벽하지가 않습니다.
그렇다면 공차가 발생하는 이유는 무엇일까요? 일반적으로 강 재질의 소재를 가공하는 과정 즉 깎는 과정에서 X,Y,Z 축으로의 흔들림으로 인한 오차가 발생할 수도 있고 가공 툴의 마모로 인한 오차가 발생하는 경우, 소재의 편심이나, 뒤틀림, 평탄도 등으로 인한 오차가 발생할 수 있고, 똑같은 소재 100개를 가공하더라도 1~100의 가공 소재의 오차가 발생할 수도 있고, 인적 요인도 있을 수 있고, 재료의 가공성, 누적 공차 등 여러가지 요인들이 산적해 있습니다. 다시 말해 여러 가지 복합적인 오차들로 인해서 결과물인 가공 소재에 공차가 발생하게 되는 것이지요.
치수 공차를 관리해야 하는 이유
공차 관리 이해를 위한 간략한 가공 및 설계 및 가상의 가공을 진행해 보겠습니다.
STEP 1.
- 첫 번째 부품으로 아래 그림과 같이 직경이 Ø100에 길이가 100L 인 환봉을 하나 그렸습니다.
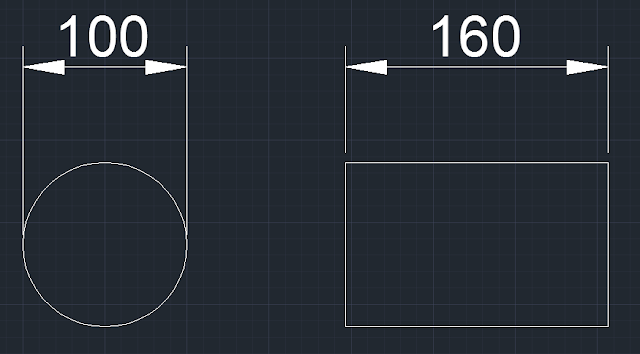
STEP 2.
- 두 번째 부품으로 아래 그림과 같이 가로세로 길이가 200인 정사각형의 중심에 Ø100 Hole을 가공하겠습니다. 전체 길이는 160Lmm 입니다.
STEP 3.
- 두 개의 부품이 완성 되었습니다.
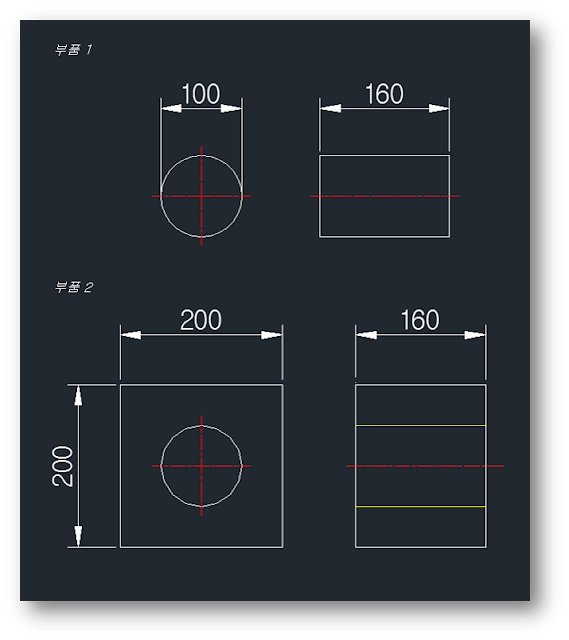
STEP 4.
- 두개의 부품을 도면상에서 조립해 보겠습니다. (우측면도 기준)
- 두개의 부품이 도면상으로 이상없이 조립(축과 구멍)되는 것을 확인할 수 있습니다.
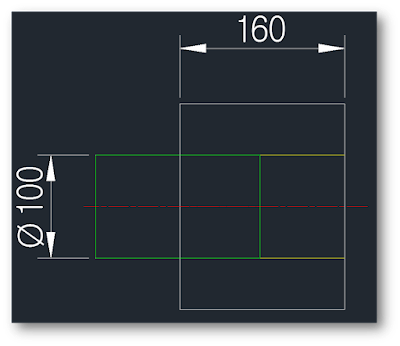
STEP 5.
- 두개의 가공품을 공차 관리를 하지 않은 상태로 가상의 가공을 실시하고 아래와 같은 결과를 얻었습니다.
- 부품 1번은 설계상 정 치수가 Ø100mm 이었으나 가공 후 Ø99.82mm
- 부품 2번은 설계상 정 치수가 Ø100mm 이었으나 가공 후 Ø99.52mm
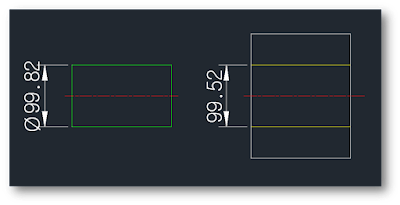
STEP 6.
- 이번에는 두개의 가공물에 대해 공차 관리를 통해 조립성을 확보해 보겠습니다.
- 각각의 부품에 대한 공차를 기재하였습니다. (끼워 맞춤등 일반적인 기준에 의한 것이 아닌 이해를 돕기 위한 임의의 치수를 사용함)
- 부품 1에 대한 가공 공차는 외경 Ø100 을 기준으로 하여 최대 -0.1mm, 최소 -0.2mm 의 허용 공차를 설정하였습니다. (허용 치수 99.8~99.9mm)
- 부품 2에 대한 가공 공차는 내경 Ø100 을 기준으로 하여 최대 +0.2mm, 최소 +0.1mm 허용 공차를 설정하였습니다. (100.1mm~100.2mm)
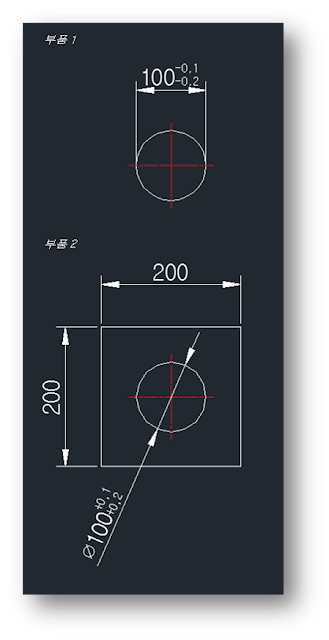
STEP 7.
- 부품 1,2의 가상의 가공을 통해 아래와 같은 결과를 얻었습니다.
반도체설비와 같이 정밀한 기계류를 생산하기 위해서는 그 만큼의 정밀한 공차 관리가 필요합니다. 가공업체도 반도체 장비 가공품을 전문으로 하는 곳이 있고 그렇지 않은 경우는 일반 산업 기계를 전문으로 하는 곳으로 나눌수 있습니다. 가공에는 여러가지 변수를 수반합니다. 소재의 상태, 툴의 마모량, 기계의 사용연한에 따른 마모 등 공차 변수가 많이 발생합니다. 정밀한 공차 관리가 필요할 경우 그 만큼 실력있는 가공업체에 맡겨야 하고 이는 가격적인 부분에 상승요인으로 작용하게 됩니다. 실제로도 가공업체의 역량에 따라 공차 및 품질에 차이가 있다는 것을 경험하게 됩니다. 공차는 특정 가공 소재의 크기에 비례하게 됩니다. 예를 들어서 길이가 100mm 인 환봉의 길이 공차 보다는 3,000mm 인 환공의 길이 공차가 더 커지게 됩니다. 설계 할 때 공차 관리를 위해서는 기본적인 기준이 필요 합니다. 아래 에서는 몇가지 참고할 만한 내용의 자료를 나열하였습니다. 하지만 공차를 책에 나와 있는 기준에 맞추어 작성하였다고 해서 100% 맞지 않는 다는 점에 주의할 필요가 있습니다. 예를 들어서 특정 구멍에 볼 부쉬를 끼워 넣을 경우 도금의 두께 등을 고려해서 0.05~0.03의 공차를 적용하는 것을 예로 들 수 있습니다. 이러한 것을 경험에 의한 공차라고 하는데 현업에서는 이러한 일이 종종 발생하게 됩니다. 따라서 공차 설계의 기준은 편람에 나와 있는 내용으로 하되, 경험있는 설계자의 확인이 필요하다는 것을 기억해야 겠습니다.
설계 참고 자료 몇가지
* 일반 산업기계 가공품의 치수 공차
치 수
|
허용공차
|
|
1 초과
|
4 이하
|
± 0.1
|
4 초과
|
16 이하
|
± 0.2
|
16초과
|
63 이하
|
± 0.3
|
63 초과
|
250 이하
|
± 0.5
|
250 초과
|
1,000 이하
|
± 0.8
|
1,000 초과
|
2,000 이하
|
± 1.0
|
2,000 초과
|
4,000 이하
|
± 1.5
|
4,000 초과
|
8,000 이하
|
± 2.0
|
8,000 초과
|
16,000 이하
|
± 2.5
|
각 도
|
± 0.5
|
**용접 구조물의 치수 공차
구 분
|
치 수
|
허용공차
|
|
치 수
(SIZE)
|
100 이하
|
± 1.5
|
|
100 초과
|
300 이하
|
± 2.0
|
|
300 초과
|
1000 이하
|
± 3.0
|
|
1000 초과
|
3000 이하
|
± 5.0
|
|
3000 초과
|
5000 이하
|
± 7.0
|
|
진 직 도
|
300 이하
|
± 1.5
|
|
300 초과
|
1000 이하
|
± 2.5
|
|
1000 초과
|
2000 이하
|
± 3.5
|
|
2000 초과
|
3000 이하
|
± 5.0
|
|
3000 초과
|
5000 이하
|
± 7.0
|
**상용하는 부품의 끼워맞춤 공차
부품명 혹은 조건
|
구 분
|
기 호
|
적 용 예
|
|
전동기의 축
|
상대내경
전동기 축
|
H6
m6
|
커플링, 브레이크풀리
치차 등
|
|
KEY
부착 축
|
일반의 경우
|
내경
상대 축
|
H6
m6~n5
|
|
웜 휠
|
내경
상대 축
|
H6
h6
|
||
분할형 커플링
|
내경
상대 축
|
H7
h6
|
||
일체형 BUSH
|
BOSS 내경
BUSH 압입후
상대 축
|
H7
H8
d8
|
ROPE SHEAVE
차륜
|
|
분할형 BUSH
|
BOSS 내경
BUSH 외경
BUSH 내경
상대 축
|
H7
h6
H7
d8
|
||
굴름베어링
관련 맞춤
|
내륜 회전
|
내경
상대 축
|
H6
k6
|
|
외륜회전
(경부하)
|
내경
상대 축
|
J6
h6
|
||
외륜회전
(중부하)
|
내경
상대 축
|
K6
h6
|
||
베어링용 Collar
|
상대 축
|
d8
|
||
SHEAVE용 중공축
|
상대 축
|
f7
|
||
Collar 와의
끼워맞춤
|
축의공차가 +경우
|
칼러 내경
|
E7
|
|
일반의 경우
|
내경
상대 축
|
H7
h6
|
||
오일 씰과의
끼워맞춤
|
BOSS 내경
|
내경
|
H7
|
|
축 혹은 칼라
|
외경
|
d8
|
||
Pin 과
Pin Hole
|
일반의 경우
|
내경
상대 축
|
H8
d8
|
|
큰 틈이 필요한
경우
|
내경
상대 축
|
H10
d8
|
||
미끄럼운동부
|
내경
상대 축
|
H7
f7
|
'기계설계 자료&계산서' 카테고리의 다른 글
덕트 설계(전원선,통신선,공압선) 설계 적용방법 (0) | 2023.10.24 |
---|---|
기계 가공품 열처리 방법 6가지 (0) | 2023.10.24 |
기계 가공품 표면처리 방법 6가지 (0) | 2023.10.24 |
다듬질기호의 도면 적용 범위 (0) | 2023.10.24 |
가공방법에 따른 사상정도 구분 및 도면표기 법 (0) | 2023.10.24 |
댓글