반응형
A. Plant & Facility Layout

<Piping Layout - 출처 ayoqq>
레이아웃이란?
레이아웃의 사전적 의미는 어떠한 특정 물체를 둔다.
플랜트를 포함한 자동화 공장, 수처리 시설, 자동차, 반도체, 등
대규모 설비 집약체 즉 공장을 짓는 과정 중 레이아웃은
필수적인 도면 요소입니다.
레이아웃을 바탕으로 설비 배치 및 Construction 등의
후속공정에 착수할 수 있습니다.
레이아웃은 제한된 혹은 설정한 범위(Range)안에 요소를
올바르게 배치하는데 그 목적이 있습니다.

레이아웃의 사전적 의미는 어떠한 특정 물체를 둔다.
즉 배치한다는 뜻을 가지고 있습니다.
우리가 흔히 레이아웃 혹은 레이아웃 Drawing 이라고 하는 것은 결국
배치, 배치도면과 같은 말입니다.
이를 확정해서 전문적으로 표현하면 다음과 같습니다.
레이아웃이란 제조, 생산 및 기타 필요로 하는 모든
시설의 목적에 필요한 항목들을 정리한 것으로 생산에
적합한 활동을 수행할수 있도록 기기 및 부대 시설을
포함한 생산활동에 필요한 모든 요소를 올바르게 배치한 것
용어를 적용하는데는 제한적이지 않습니다.
특정 요소의 배치가 필요한 모든 구간에
레이아웃이라는 용어를 적용할 수 있습니다.
예를 들면 아래와 같이 말이죠.
**플랜트 시설과 같이 규모가 큰 공장의 경우에는 Plot plan 용어를 사용하기도 합니다.
레이아웃 Drawing 은 Design & Engineering 단계에서
- Plant layout drawing
- Piping layout drawing
- Facility layout drawing
- Product layout drawing
- Process layout drawing
- Instrument layout drawing
- Panel layout drawing
**플랜트 시설과 같이 규모가 큰 공장의 경우에는 Plot plan 용어를 사용하기도 합니다.
레이아웃 Drawing 은 Design & Engineering 단계에서
선행되어야 하는 매우 중요한 역무입니다.
통상적으로 레이아웃 도면은 새로 그리는 것을 원칙으로 하는데
기존에 유사하게 적용했던 사례(Reference) 가 있을 경우
이를 참조해서 적합하게 되므로 조금은 수고스러움을 덜 수 있습니다.
원 발주처에서 정해준 부지 사이즈 (Area) 에 맞추어
진행하는 방식과 설비에 맞추어 부지 사이즈를 정하는 방식 두 가지로 나뉘어 집니다.
후자의 경우는 설비를 자유롭게 배치한 후 필요한
전체 면적을 결정하는 Bottom-up 방식으로 보다 창의적이고
적합한 형태의 배치가 가능합니다.
하지만 현업에서는 제한된 공간이 주어지고 이를 바탕으로 레이아웃을
진행하는 Top-down 방식의 적용이 대부분 입니다.
레이아웃 작업은 규모에 따라 차이가 있으나 보통 한 번에 끝나지 않고
여러 번의 반복 수정 작업을 거치게 됩니다.
이는 초기에 확정되지 않은 설비와 요소들이 단계별로 확정되고
이를 반영하는 작업을 반복적으로 수행해야 하기 때문이죠.
레이아웃은 초기에 신속하게 확정하는 것이 매우 중요합니다.
이를 바탕으로 들어갈 요소 및 기자재의 크기가 결정하거나
전체 면적을 확정 해야하기 때문이죠. 레이아웃의 잦은
변동사항은 설계 변경 및 자재 물량에 영향을 미치게 되며
긍정적인 효과를 기대할 수 없습니다.
이러한 이유로 레이아웃 작업은 초보자가 아닌 공정
전체에 대한 이해도가 높은 숙련자를 통해 진행하는 것이 일반적입니다.

<Layout Drawing 출처 Ayoqq>
레이아웃의 잦은 변경 사유
레이아웃이 단 한 번에 신속히 확정되면 얼마나 좋을까요?

레이아웃의 잦은 변경 사유
레이아웃이 단 한 번에 신속히 확정되면 얼마나 좋을까요?
그런데 그렇지 못하는 데는 몇 가지 이유가 있습니다.
초기에 셋팅한 레이아웃은 완벽하지 않은 상태 즉 Priminary Drawing 입니다.
- 설비의 용량이나 크기가 변경된 경우 : 레이아웃 작업 담당자는 신속히 변동사항을 확인하고 레이아웃의 Area 에 영향이 있는지를 검토해야 합니다. 만약 제한(Limit)치를 초과할 경우 이를 신속히 보고하거나 공유하여 대책을 마련해야 합니다.
- 공정에 변동사항이 있는 경우 : 레이아웃 담당자에게 날벼락과 같은 일입니다. 레이아웃 전체를 다시 점검하고 일일이 확인해야 합니다.
- 기타 : 발주처 요구사항 반영, 생산 품목의 변화
초기에 셋팅한 레이아웃은 완벽하지 않은 상태 즉 Priminary Drawing 입니다.
이를 완벽하게 만들어 가는 과정중에 여러가지 문제점들이 생기는데
초기에 Design 했던 공정 대비 공정 흐름상에 문제가 있는 경우,
Work 및 동선상에 거리가 너무 멀 경우, 생산 시간이 예측 대비 초과하는 경우가 있습니다.
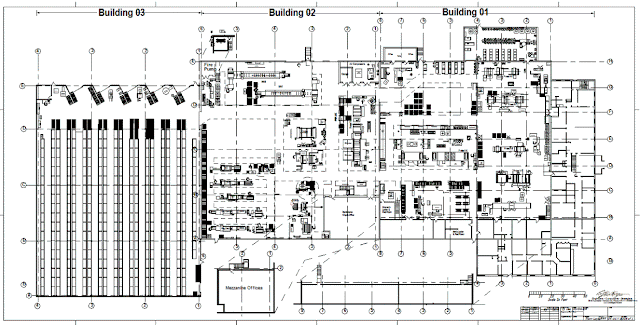
레이아웃 작업시 고려해야 할 사항
레이아웃 작업 시 고려해야 할 부분은 어떠한 것들이 있을까요?
먼저 중요한 두 가지는 경제성과 최적화입니다.
경제적이며 공정 흐름이 완벽히 반영된 배치도가 좋다는 것은 누구라도 동의할 수 있습니다.
예를 들어 Worker 의 이동이 없는 구간에 불필요하게 Door를
설치한다거나 공정의 흐름을 잘 못 이해하여 기기별 배치를
역으로 배치한다거나 공압 Line 이 너무 멀리 떨어져 있어서
배관 자재를 추가로 구매해야한다거나,
세세한 부분까지 신경 써야 할 것이 많은 것이 사실입니다.
레이아웃을 어떻게 그릴 것인지에 대한 정형화된 규칙은
없으나 공통적으로 지켜야 할 몇가지 사항들은 존재 합니다.
글쓴이가 생각하는 협업이 필요한 레이아웃 작업 시 가장 필요한 사항은
- 유지 보수 및 동선 확보 (작업자 접근성 및 작업성 확보)
- 안전 (위험요소 검토)
- 추가 공간 고려
- 통일감
- 불필요한 공간 확인 (필요시 삭제)
- 설비 배치에 혼잡성이 존재 하는지
- 유체를 사용하는 설비가 포함되어 있는 레이아웃의 경우 물을 배수할 수 있는 Trench 위치 확인
- 향 후 추가적인 설비 도입 계획이 있다면 가용 면적의 확인
- 대형 장비의 초기 설치를 위한 동선 및 문제점 파악
- 전원선, 통신선, 유틸리티 선의 덕트 레이아웃
- 펜스(Fence) 설치 범위 및 위치 확인
- 토양 상태 및 배수, 트럭 및 서비스의 접근성과, 폐기물의 처리 동선
- 환기구의 위치 및 방향의 확인
- 위험 구역의 지정 및 확인 적정설비의 배치
바로 "관련 정보의 신속한 공유" 입니다.
레이아웃에 포함된 설비 및 자재, 기타 변동된 사항이 없는지
수시로 확인하고 공유하는 것이 레이아웃 작업을
조속히 마무리 하는 것이고 앞선 설명에서 처럼 후 공정에서
잦은 변화에 의한 영향을 최대한 줄이는 것을 목표로 해야 합니다.
B. 자동화 설비 레이아웃의 구성

자동화 설비 레이아웃의 구성
자동화 설비란 특정 제품을 전용 기계를 이용하여 일률적으로
대량생산의 목적의 설비로 정의합니다.
자동화 기계 공정은 5가지 구역(Block)으로 구분하며
이를 통해 자동화 설비의 효율성과 제어 수준을 설명할 수 있습니다.
Block 1. 적재 구역
적재 구역에서는 재료의 생산을 위한 자재가 1차 가공 형태 혹은
원자재 형태로 공급되며 이를 로딩하기 위한 적재
시스템과 무게의 측정, 부품의 방향 결정, 이송 시스템과
같은 프로세스를 처리할 수 있게 구성됩니다.
자동화 설비를 통한 생산 레이아웃의 가장 첫 지점으로
조립 혹은 가공을 위한 **Work 의 도킹을 주 목적으로 합니다.
(**Work 란 자동화 설비의 생산 대상물을 지칭합니다)
Block 2. 기능 구역
기능 구역이란 Work 를 조립하거나 소성 변형, 용접, 압입, 접착과
같은 공정을 처리하는 것으로 로보트를 이용한 자동 용접 구역이나,
자동 샤프트 압입 공정과 같은 자동 처리 공정을 예로 들 수 있습니다.
실질적인 제품의 생산이 이루어지는 곳으로 자동화 설비에서
설비 유효성과 생산량, 택 타임을 결정하는 가장 중요한 구간입니다.
Block 3. 점검 구역
검사 구역은 적재, 기능 구역을 통과한 제품의 상태를 점검하는 구역으로
정의하며 제품의 상태를 평가합니다.
예를 들어 용접 상태, 압입 상태, 마모 상태를 설계치와 대조하여
비교한 후 전 공정의 유효성을 평가합니다. 점검 구역은
전체 공정의 안전 상태를 점검할 수 있는 과정입니다.
점검 방식은 센서(포토센서, 광센서)를 이용한 비 접촉 방식과
사람이 샘플링 검사를 수행하는 접촉 검사 방식으로 구분합니다.
접촉 방식에서는 실질적으로 생산 제품의 상태를 눈으로 확인하고
측정하여 결과를 산출 합니다. 점검 구역은 기능 구역의
중간 혹은 은 배출 구역 전단에 배치할 수 있습니다.
Block 4. 배출 구역
배출 구역은 기능 구역에서 생산한 품목을 위치에서 해제하여
다른 공정 혹은 운반구역으로 이동하기 위한 준비를 하는 구역으로 정의합니다.
자동화 설비의 규모가 크고 셀 단위당 공정이 연동의 목적을
갖고 있을 경우 배출 구역은 다른 기능 구역과 연동 될 수 있습니다.
Block 5. 운반 구역
운반구역은 제조공정에서 생산된 제품의 반제품 혹은
완제품의 이동을 위한 구역으로 정의합니다.
내용정리

자동화 설비의 레이아웃은 적재/기능/점검/배출/운반 5가지의 구역(Block)으로 구분합니다.
각 블럭은 고유의 목적을 갖고 있다는 점을 기억해야겠습니다.
Inside Insight 였습니다.
INSIDE INSIGHTS ENCYCLOPEDIA
반응형
'엔지니어링 기술자료' 카테고리의 다른 글
Leak test(누설시험) 검교정 성적서가 중요한 이유와 Report 공통사항 (0) | 2023.11.16 |
---|---|
모터 Enclosure type 7가지 (0) | 2023.11.16 |
펌프 축동력(Brake horse power)과 모터 용량(Motor power) 구하는 방법 (0) | 2023.11.15 |
펌프 유량과 팽창계수 관계 (0) | 2023.11.15 |
Once Through Cooling Water - 일회 냉각 방식이란 (0) | 2023.11.15 |
댓글